Robots help fill gaps in Minnesota's workforce
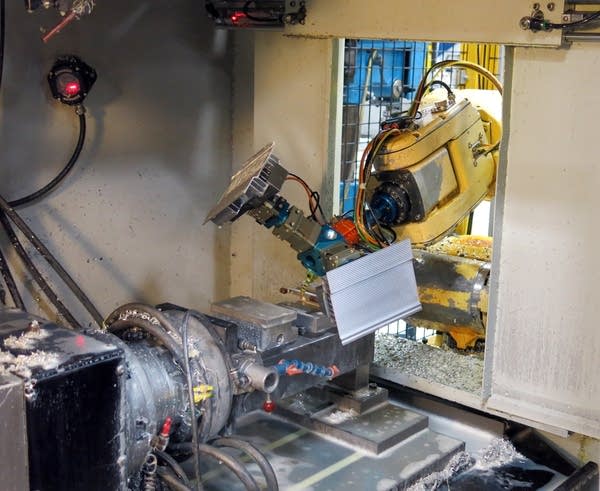
Go Deeper.
Create an account or log in to save stories.
Like this?
Thanks for liking this story! We have added it to a list of your favorite stories.
Outside Cosmos Enterprises, the big "now hiring" sign is pretty much a permanent fixture.
Robert Grove, who owns the small machine shop, is constantly looking for skilled people to build parts for other manufacturing companies. But he said skilled machine operators are "almost impossible" to find in Elbow Lake, population about 1,200.
Grove, who has 23 employees, trains most of the workers he hires because it's hard to find skilled workers who will move to a small town.
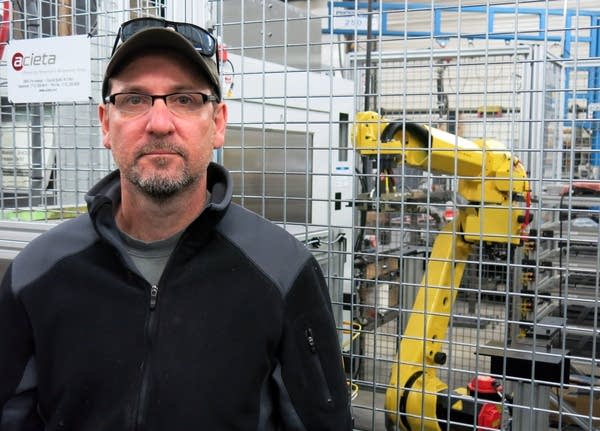
"Not only is there a lack of skilled workers, there's just a lack of workers," he said. "We got to start adapting and figure out what to do."
Turn Up Your Support
MPR News helps you turn down the noise and build shared understanding. Turn up your support for this public resource and keep trusted journalism accessible to all.
A few months ago, Grove found a solution. He invested nearly $250,000 in a robot that can handle many of the repetitive tasks in his shop.
He isn't the first to do so. A growing number of manufacturers in Minnesota are turning to robots to help ease a labor shortage.
Robots aren't new in large manufacturing plants, but small companies across Minnesota also are embracing a new generation of robots to stay competitive.
In Grove's brightly lit shop, the robot sits in a cage to keep workers from walking into the rapidly moving arm. The robot's job is to load metal blocks into computerized machine tools that shape the parts. It then removes the finished part — all without ever eating lunch or taking a bathroom break.
"For sure you gain 45 minutes a day of production," Grove said. "That's real money."
Grove said the robot doubled the output of two milling machines. It also allows his skilled workers to focus on using their skills, instead of simply loading parts into a machine all day.
Although there was a steep learning curve for workers who need to work with the robot, Grove is convinced his company won't survive without embracing automation.
"It's going to get worse as far as I'm concerned, just with the baby boomers retiring," he said. "I mean, there's a ton of skilled people retiring every day."
Grove already is thinking about adding a second robot.
Thirty minutes away, Alexandria Industries has more than a decade of experience with robots. The company, which makes aluminum parts for everything from medical equipment to military rifles, is a much bigger business, employing about 370 workers.
"We have nine robots tending machines today," engineer Todd Carlson said recently. "I've got two more robots on order right now and scheduled to order two more before the end of the year."
Carlson said robots have a checkered history at the company. In 2001, the company purchased its first, Rosie, to make parts for the telecommunications industry. After the dot-com bubble burst, the contract disappeared and the nearly $500,000 investment sat unused.
"For four or five years we were pretty disappointed with robotics," Carlson said.
But robots have changed. New versions are easier to program and more adaptable to different jobs.
Carlson said robots have not replaced workers and no one lost their job. But the company has been able to expand despite a perpetual labor shortage.
"It's a tough labor market out there and automation is really helping us through that," he said.
Having robots do repetitive tasks, Carlson said, makes for happier workers.
"They don't like loading parts. They like troubleshooting, they like problem solving," he said. "So it really changes the level of operator we're able to attract and it really gives them more satisfaction in the job that they're doing."
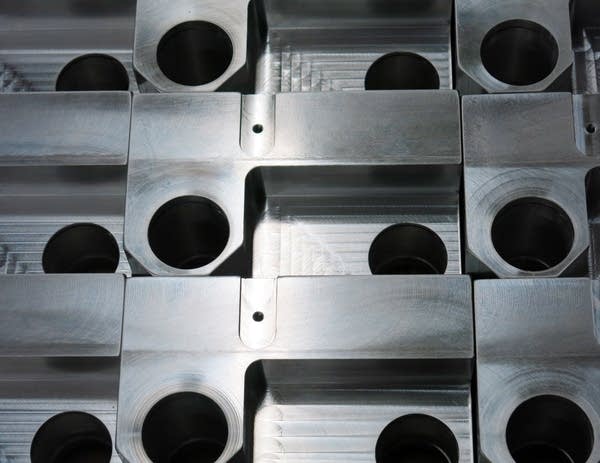
A workday full of repetitive tasks could explain why many Minnesota manufacturing companies have a hard time finding workers.
A survey conducted last year by the business-consulting firm Enterprise Minnesota found 67 percent of companies reported difficulty in filling open positions.
Bob Kill, president and CEO of Enterprise Minnesota, sees more small companies — especially in rural communities — asking questions about automation.
"I think the challenge is it's a dwindling workforce," Kill said. "The market is forcing companies of all sizes to automate where they can and we're going to continue to see automation of all kinds of types continue to grow."
About 45 percent of manufacturing in Minnesota happens outside the Twin Cities metro area, Kill said, and many of those companies have no choice but to focus on efficiency.
Mark Sagedahl, who teaches robotics at Alexandria Technical and Community College, advises companies to use robots.
"Ten years ago, 15 years ago, the big trend was outsource because we could do it cheaper, faster overseas somewhere else because of the labor costs, and the big thing was the labor costs," Sagedahl said. "The problem, the issue, that manufacturing saw was that the quality isn't there."
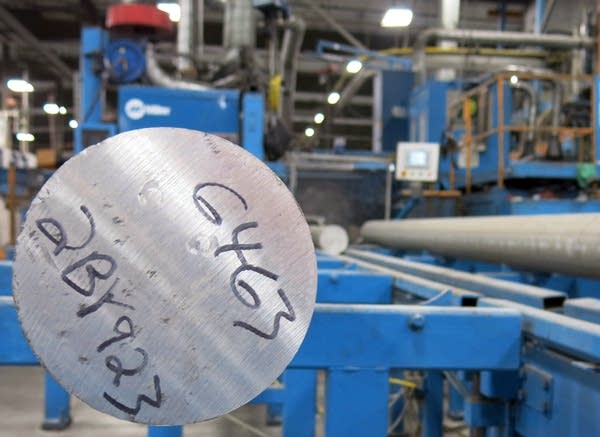
So some of the work that might have occurred shipped overseas is returning to U.S. companies.
Sagedahl, who also helps design robot training programs for companies, said 10 years ago it took computer programming skills to run a robot. But these days, he said, anyone who can use a smartphone can learn to operate the new generation of smarter robots.
The expanding use of robots, he said, might convince more young workers to consider manufacturing jobs.
"Now, what they've really gone to is the idea of that robot is almost an extension of a person," Sagedahl said. "It has multiple skillsets. It has multiple abilities depending on the needs."