On the Iron Range, a push for a new kind of iron
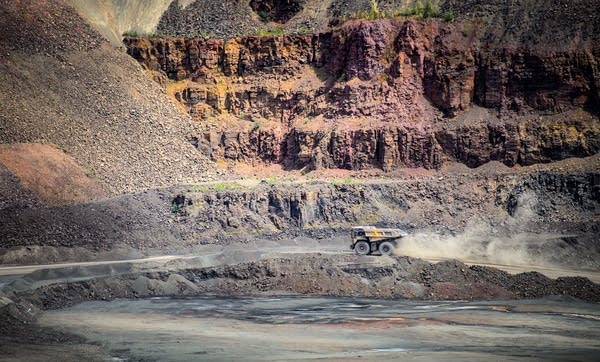
Like this?
Log in to share your opinion with MPR News and add it to your profile.
Like this?
Thanks for liking this story! We have added it to a list of your favorite stories.
For more than a century, iron ore mined from Minnesota's Iron Range has fed enormous blast furnaces at steel mills around the Great Lakes in old rust belt cities like Chicago, Detroit, Cleveland and Hamilton, Ontario.
After the iron ore is combined with coal and limestone in 12-story-high stacks, the mixture is heated to more than 2,600 degrees to create the molten iron needed for steel. That steel has helped manufacture everything from toy wagons to pickup trucks.
But in the few months since steel companies on the Iron Range laid off about 1,000 mineworkers — one out of every five workers in a region where mining makes up about a third of the economy — two trends in the steel industry have Iron Range watchers feeling uneasy.
Even as officials contend with the current downturn, many worry about a longer-term question with even larger economic consequences. At issue is whether Minnesota is producing the right kind of iron ore product for a changing steel industry.
Support the News you Need
Gifts from individuals keep MPR News accessible to all - free of paywalls and barriers.
First, the blast furnaces that Minnesota taconite pellets feed are disappearing, said Brian Hiti, a senior policy adviser on mining for the Iron Range Resources and Rehabilitation Board. Since 2006, he said, the number of blast furnaces in the United States has fallen from 28 to 21.
"The tonnage of steel produced in those blast furnaces has been reduced by about 10 million tons," Hiti said.
The last new blast furnace in the United States was built in the 1970s. These days, steel companies like fast-growing Nucor are instead building electric arc furnaces, "mini mills" that use scrap metal or a more pure form of iron than taconite pellets. They're a lot more flexible and efficient than blast furnaces.
"That's kind of the [bogeyman] that's out there," Hiti said. "The growing part of the market is the electric furnace market."
The new market uses about 60 percent of the steel produced in the United States.
"So you have to be looking to where your customer is going and make sure you provide a product that they can use," Hiti said.
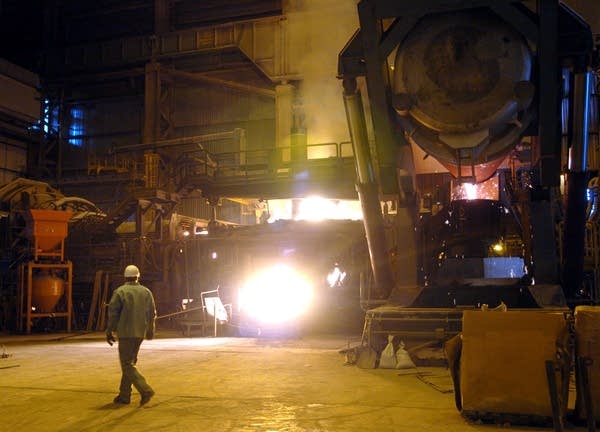
The No. 2 worry of mining industry watchers in northern Minnesota is how the mills will be affected by the Ford Motor Co.'s decision to build the F-150 pickup with a high-strength, military-grade aluminum alloy body.
Don Fosnacht, a metallurgical engineer at the Natural Resources Research Institute at the University of Minnesota Duluth, estimates that building Ford's flagship pickup out of aluminum displaces about 500,000 tons of iron ore pellets a year.
"If other trucks go that way because of the highway fuel economy standards, you could displace another 1.8 million tons very easily in model year 2018, 2019," he said.
As the market for steel changes, Fosnacht said, Minnesota's mining industry needs to change with it.
"You know these things aren't going to just go away," he said. "They're actually big time events that will dramatically impact our iron ore industry. So we have to be nimble on our feet. ... How are we going to address them to have a viable industry for the future?"
The solution, he and others say, is to produce a new kind of iron that can be used in electric arc furnaces.
The product most are considering is called direct reduced iron, a purer form of iron than lower-grade taconite pellets that can be used directly in electric arc furnaces. But it requires more processing.
Cliffs Natural Resources recently completed a pilot project at its Northshore Mining plant in Silver Bay, Minn., that successfully produced 30,000 tons of specialized pellets that can be used to make direct reduced iron. The Iron Range Resources and Rehabilitation Board gave the company a $1.6 million rebate for the pilot project through its Mining Reinvestment Fund.
The pellets would still have to be sent to a separate plant to make direct reduced iron before it's shipped to steel mills.
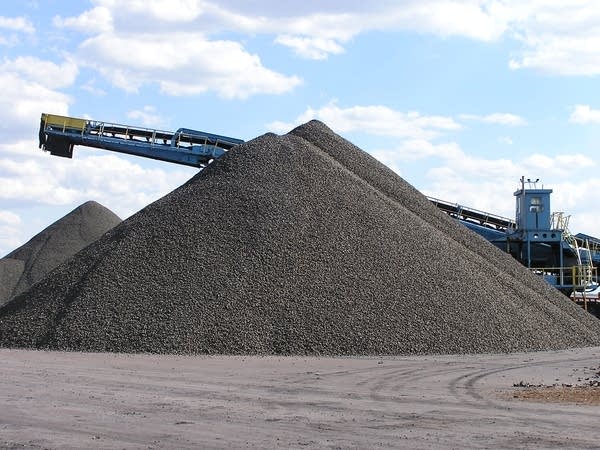
Cliffs has not provided details, but in a call with investors this spring CEO Lourenco Goncalves said the company also is exploring building the state's first direct reduced iron plant. He said the company is working with Minnesota officials so it can put in place the first facility in the state to supply Midwest mini mills with direct reduced iron pellets.
Essar Steel, which is building a new mine and pellet plant on the Range, also has long term plans to make the special pellets and build a direct reduced iron plant on site. It also may build an electric arc furnace.
U.S. Steel, which operates two huge mines on the Iron Range, recently announced plans to build its first electric arc furnace in Alabama.
Making steel, or a richer form of iron, directly on the Iron Range, has long been the biggest economic development goal in the region.
"This is a worldwide phenomenon," said Tony Barrett, an economist at the College of St. Scholastica. "If you're in a commodity-producing area, you want to increase the value added domestically."
But it's a goal the Range has struggled to achieve, Barrett said.
"It's moved very, very slowly, slower than I would have thought," he said. "So there must be some question about profitability. That's one thing about capitalists — if they're not doing it, it's probably not profitable."
A factor that may eventually change the economics is access to cheap energy. A lot of natural gas is required to turn low grade iron ore into direct reduced iron and Minnesota, which has North America's largest deposits of iron ore, is very near to new supplies of gas in North Dakota and Canada.
"The problem isn't the tonnage of ore available," Hiti said. "We've got plenty of ore available. The challenge is making sure that it's produced in a form that the customer wants."
Correction (June 25, 2015): An earlier version of this article incorrectly suggested that taconite pellets had been used in steel production for more than a century.