Low-skill adults train for new opportunities in manufacturing
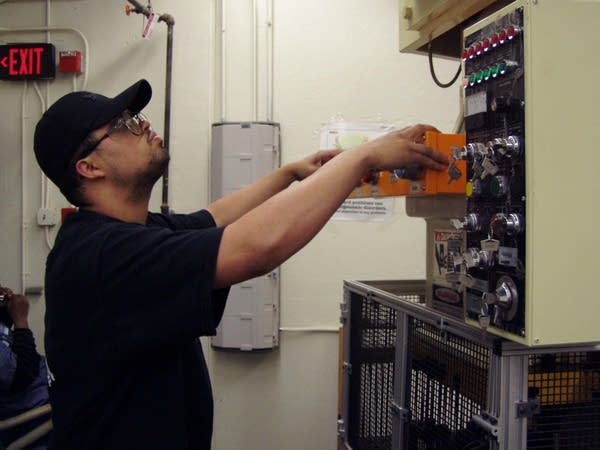
Until recently Erik Underbakke was stuck in an employment rut. He had a high school diploma and a little bit of college under his belt. But in an economy that increasingly values education, Underbakke had to settle for low pay and low-skill jobs, like delivering pizza.
"I've done about every kind of dead end job there could be," Underbakke says.
Hennepin Technical College's program for low-wage adult workers is designed to help people like Underbakke who want better-paying jobs but who are short on skills.
In a class at the college, Underbakke learns how to operate a big silver stamping machine the size of a refrigerator that's pounding two pieces of metal together. The classes in metalforming meet twice a week for four hours at a time. Metalforming involves shaping sheet metal into products and making metal stamps and parts. Students get hands-on experience operating metalforming machinery, but they also spend a lot of time in the classroom, where they receive rigorous instruction in physics and math.
Create a More Connected Minnesota
MPR News is your trusted resource for the news you need. With your support, MPR News brings accessible, courageous journalism and authentic conversation to everyone - free of paywalls and barriers. Your gift makes a difference.
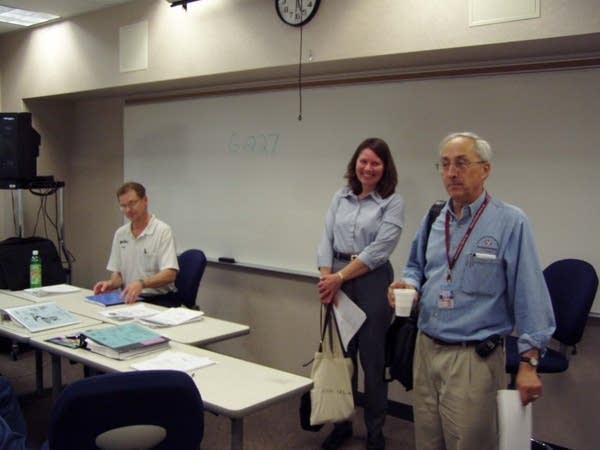
Underbakke is in the second phase of the coursework, and he says it's been tough to handle the classes on top of his full-time day job. Two things keep him going: copious amounts of Mountain Dew, and the calls from potential employers he received after just one course.
"I've never been on that end of the deal," Underbakke says. "Usually, I'm calling up, asking to set up interviews. After that, I had four or five companies asking me to set up an interview. I had to keep asking, 'Who are you again? And you want to talk to me?' I wasn't sure they had the right number." Many of the companies seeking out people like Erik Underbakke are, like him, trying to put their own histories of low-skill, low-paying work behind them.
Joe Fredkove, who oversees training and business development programs at Hennepin Tech, says outsourcing is a major reason. Critics have accused employers of killing American jobs by moving work to countries with lower wages. But Fredkove says now outsourcing is creating some job opportunities in American factories.
"What's happened is some companies have outsourced jobs that are minimal in skills and technology. And in order to compete in the global marketplace they've had to add value. And the way to do that is better technology and more highly skilled individuals," he explains.
Some companies have outsourced jobs that are minimal in skills and technology. And in order to compete in the global marketplace they've had to add value. And the way to do that is better technology and more highly skilled individuals.
The Hennepin Tech program is one of two pilot programs in the country. Both focus on training workers in metalforming because many small- to medium-sized companies in that industry need help finding workers with the right skills.
The pilot programs get some funding from the National Association of Manufacturers. The NAM says the skilled worker shortage is widespread across the manufacturing sector. Phyllis Eisen, a vice president with the trade organization, says huge numbers of skilled workers are retiring and need to be replaced.
"Almost 90 percent of our companies, and we represent 14,000 companies, tell us they're deeply concerned they can't find the skilled labor they're going to need to be competitive in the future," Eisen says. "So one of the things we wanted to do was highlight programs like this-- [which] are crucial to finding that skilled labor."
In its 18 months of operation, the Hennepin Tech program has trained about 100 students in metalforming. Better than 80 percent now have jobs. Graduates earn more than $13 an hour on average. Their wages rise dramatically with additional training.
The program is entirely free for the students; it's funded through a combination of public money and industry-related grants. But it's also highly selective. Hennepin Tech's Joe Fredkove says candidates have to go through eight hours of in-depth assessment tests, a regime which puts off many prospective students right away.
"They'll say, 'You know, this is way over my head. And I don't really have the aptitude or the interest.' And that's fine. Because our goal is to invest energy and money and resources into those that are going be there the last night to graduate," Fredkove explains.
Some candidates for the program are referred by a social service agency that helps disadvantaged workers, and which is a partner with the program. Other students are new workers at companies that want them to get training.
Hennepin Tech is doing a lot to publicize the program to local manufacturing companies, including bringing firms in. The college recently held a job fair, but not the typical kind. This time, the companies were trying to make an impression more so than the job candidates.
In her pitch, Elizabeth Abraham, CEO of Top Tool Company in Minneapolis, told students there's a bright future in the factory sector.
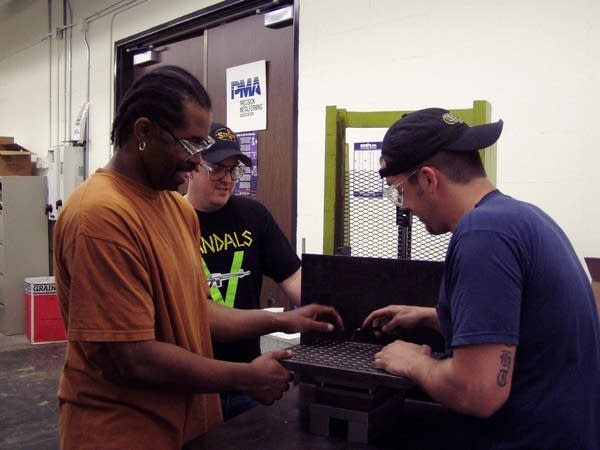
"Manufacturing is a great door to enter now," she said. "We're requiring people to have high technical skills. Instead of a trade, we're looking at tool and dye as a profession.
Abraham also touted her company's wages and benefits.
"At Top Tool we don't have any minimum wage jobs. Tool and dye makers at a minimum make $50,000 a year, and some make over $100,000. Our press room people start at $30,000," said Abraham. "We have health care for every full-time person and their family."
All those benefits sound good to Danny Brown, who's been working his way through the metalforming program while raising a family.
"I'm a single dad of two teenage boys," he says with a big sigh. "It gets kind of rough Tuesday nights and Thursday nights, but we work it out."
Program officials say Brown is typical of the students in the program. He needs the benefits the training offers and has the perseverance to keep coming on those difficult Tuesday and Thursday nights.
In the fall, the program will expand, with the hope of training another 150 workers over the next three years.