The big question: Why did the bridge fall down?
Go Deeper.
Create an account or log in to save stories.
Like this?
Thanks for liking this story! We have added it to a list of your favorite stories.
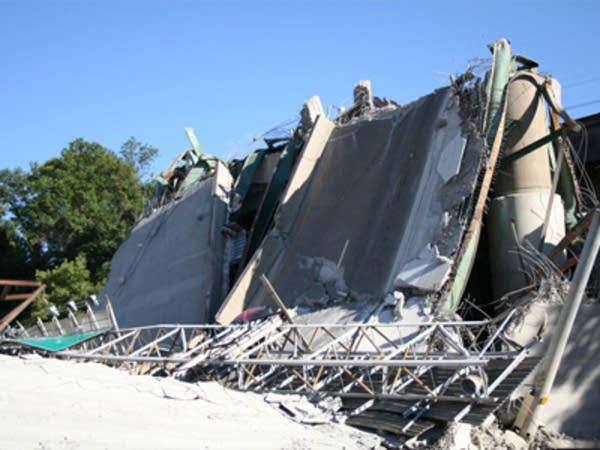
When the 35W bridge collapsed last week, it was 40 years old. It was classified structurally deficient, and the Minnesota Department of Transportation moved to inspect the bridge each year. But it did not consider the bridge dangerous.
The day after the collapse, MnDOT's state bridge engineer Dan Dorgan said he was as stunned as anyone else.
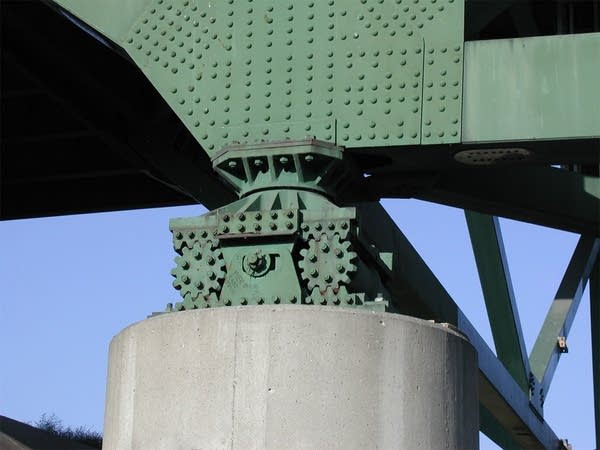
"In light of what happened, you know I would say we thought we had done all we could. Obviously something went terribly wrong," said Dorgan. "And that's going to be part of the forensic investigation for us to try to figure out what went wrong in this instance."
The National Transportation Safety Board immediately opened an investigation of the scene. NTSB Chairman Mark Rosenker said engineers are trying to learn everything they can about the bridge's condition at the time it came down.
Turn Up Your Support
MPR News helps you turn down the noise and build shared understanding. Turn up your support for this public resource and keep trusted journalism accessible to all.
"We need to have an accurate depiction of what the bridge was like at the exact moment of failure," said Rosenker. "We're also trying to determine how many cars were on there, speeds at which they were operating. Temperature. What was the temperature of the entire day."
Engineers say bridge collapses don't happen overnight. They are the result of years of use and environmental conditions.
"Bridges built in the 1950s and '60s -- they use details that are not good for fatigue fractures. That means that this bridge is 'fracture critical.'"
The NTSB will be using a complex modeling system to try out failure scenarios. But a portion of the data the agency will examine is already available.
For example, the bridge was built in 1964, and opened to four lanes of traffic in 1967. In 1965, MnDOT projected 66,000 cars would cross the bridge every day. In 2007, the daily traffic count was more than double that -- 140,000 cars and trucks. The allowable limit for truck weights also increased, from 73,000 lbs. to 80,000 lbs.
MnDOT spokesman Bob McFarlin says these changes were accounted for, and the bridge was considered functional. In 1988, the shoulders of the bridge were converted into lanes. The bridge capacity doubled to eight lanes of traffic.
"While the bridge in 1967 was striped for two lanes of traffic in either direction, the bridge itself from width to width is built to accommodate traffic the whole length of the bridge," said McFarlin. "So there didn't have to be any structural changes to the bridge."
The 35W bridge was a welded steel truss bridge. It is one of many bridges built around the country in the decades after World War II.
University of California Berkeley professor Hassan Astaneh says between 1950 and 1970, bridge members -- as the support beams are called -- were welded together.
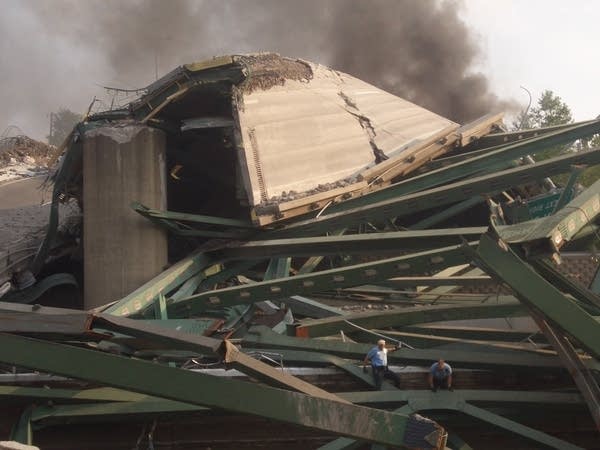
Astaneh knows a lot about bridges of this era. He served as the research arm for the California Department of Transportation in 1987, when it was dealing with a similarly troubled bridge as the 35W. He was also the primary investigator of the World Trade Center collapse for the National Science Foundation.
Bridges today aren't built with the same type of welding. But at one time, welding was considered a fast, cheap way to build.
"The designers of these bridges did not know anything about fatigue. It was during the 1970s, early 1970s, that some welded bridges built in 1950s -- they developed fatigue cracks," said Astaneh.
These cracks are hair fractures in the steel, Astaneh says, and they generally show up at the points where the steel is welded. They're caused by cycles of traffic stressing the bridge structure.
Roberto Ballarini, who chairs the University of Minnesota's department of engineering, says it isn't necessarily the weight of the traffic, but the repetition of it.
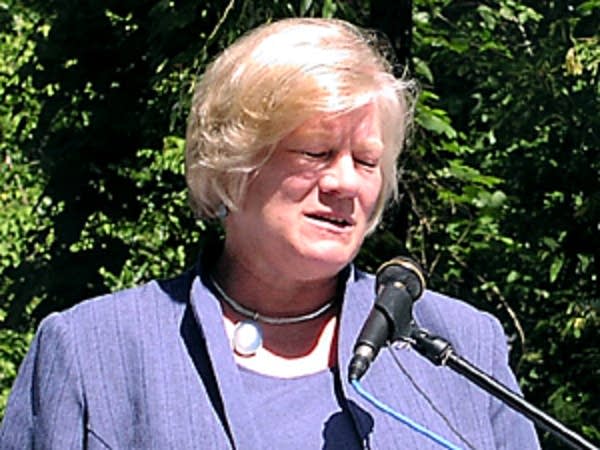
"If you take a paper clip, and if you bend it once or twice it won't break. However, if you keep repeating that over many cycles, that will actually fatigue the metal," said Ballarini. "You will first initiate those cracks, and then the cracks will propagate and you will actually break the metal into two pieces."
The 35W bridge had "numerous" fatigue cracks at various points in its spans, according to a 2006 Fracture Critical Inspection presented to MnDOT.
Astaneh says fatigue cracks are dangerous because they can weaken the structure of the bridge, and lead to failure of the entire structure. Engineers working at the time of the 35W build likely didn't know about potential cracking. But today's engineers should know.
"If you are a bridge engineer you should know," said Astaneh. "You should know that bridges built in the 1950s and '60s -- they use details that are not good for fatigue fractures. That means that this bridge is 'fracture critical.'"
MnDOT officials did recognize that the 35W bridge was 'fracture critical,' meaning that one crack could lead to others and ultimately, the bridge's collapse.
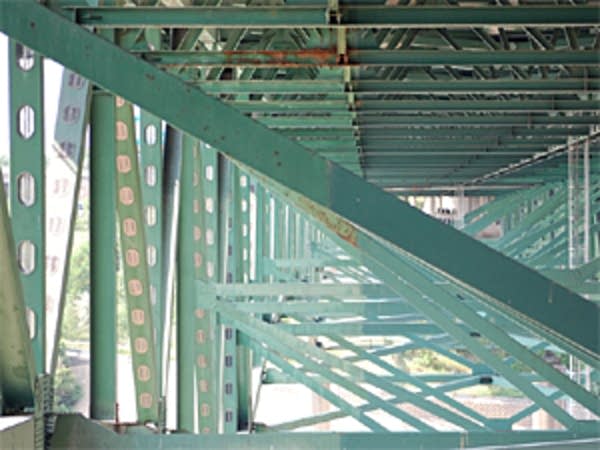
In 2006, URS Corp. completed a three-year engineering analysis of the bridge for MnDOT. It raised concerns about a main truss failure as a result of a fatigue crack.
The 35W had only two trusses supporting traffic, and 52 fatigue cracks were found in the joints. Analysts also concluded that fatigue cracks in other areas couldn't be evaluated because parts of the structure was covered in pigeon guano and were difficult to access.
Another design feature of the bridge was its lack of redundancy. Think of it as links of chain that support the weight of the bridge. Two chains provide redundancy if one of those chains has a weak link.
Transportation Commissioner Carol Molnau says the 35W bridge was structured to function safely without redundancy.
"This bridge plan, in particular, didn't have the redundancy other bridges had after that time and even before that time," said Molnau. "Because of the amount of steel and the way the bridge was designed, it was really looked at as not needing to do that."
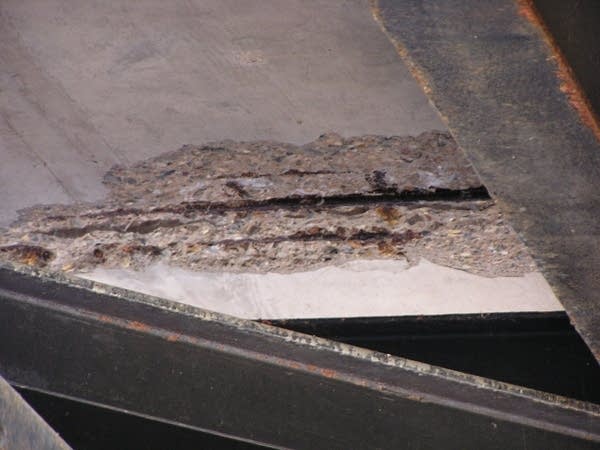
The URS reports also indicated that both the lack of redundancy and fatigue cracks were potential problems. So why weren't these more closely monitored?
Molnau says she can't speak for her predecessors, but she says her department has taken serious precautions with other bridges, like the I-494 bridge over the Mississippi River, that have shown hairline fractures in the steel.
UC-Berkeley's Hassan Astaneh doesn't cliam to know what caused the collapse of the bridge, and does not want to fault MnDOT for its failure. But he says from what observers know about the bridge, there were other warning signs.
At the time of the collapse, 18 construction workers from PCI were on the bridge. The National Transportation Safety Board is looking at the heavy equipment, including front-end loaders, the crew placed on the bridge. It's also asking about the weight, quantities of rock and other materials that sat on the bridge.
MnDOT spokesman Bob McFarlin said on that Wednesday, the crew was half finished with its job. It included resurfacing a few inches of the deck in some areas.
"In some areas of the bridge there was a complete concrete replacement, which means taking out the entire nine inches and replacing it with nine inches. And that was in eight spots along the bridge," said McFarlin.
Ripping off portions of the entire deck, professor Astaneh says, is playing with its structure. He says as a bridge weakens, the deck picks up some of the slack. It starts supporting the weight of the traffic and the bridge itself.
If a slab was removed over a fatigue crack or near an unnoticed crack, that could destabilize the bridge's delicate weight balance.
"That's not good news. That's another little storm coming in," said Astaneh. "So they're going to compound, and you're going to have all these little effects, which by themselves might not be critical to collapse the bridge."
Those little storms, as he calls them, include the heavy traffic of industrial trucks and daily commuters, the additional lanes that may have changed the balance of stress on the bridge, the fatigue cracks that were difficult to see, and the lack of structural redundancy. The bridge also faced environmental problems from water, ice and salt.
MnDOT inspection reports document that the beams of the bridge were spotted with chalking, pitting, flaking, surface rust and salt film. Astaneh says the bridge was designed to have melted snow, salt and rain run down the girders and limbs of the bridge.
Mist from St. Anthony Falls also reached the bridge and sometimes iced it over. That prompted MnDOT to install a de-icing system. But that system couldn't have protected the steel from the mist. The bridge was painted in 1968, and large portions were repainted in 1999. A complete repainting was suggested in 2006. Astaneh says if you look at the history of the 35W bridge, warning bells have been ringing. And it may be a confluence of factors that made this bridge drop into the Mississippi River.