In waste rock, mining companies find opportunity and create jobs
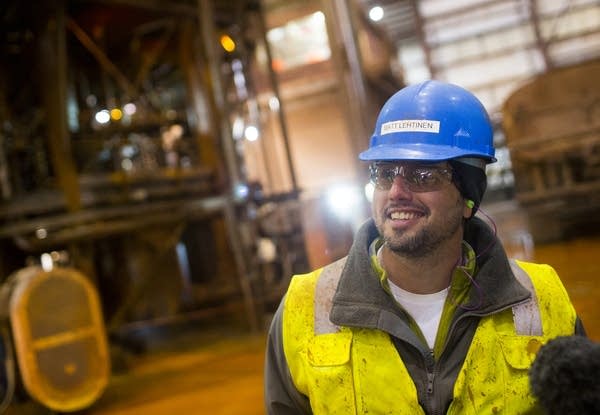
Go Deeper.
Create an account or log in to save stories.
Like this?
Thanks for liking this story! We have added it to a list of your favorite stories.
The rising price of iron ore and other metals in the last decade has led mining companies to an important discovery: There's money to be made in what was once considered waste.
Minnesota's Iron Range is littered with the legacy of 130 years of iron mining. Mine pits, enormous waste rock piles and tailings basins dot the landscape.
A newfound interest in the leftover rock is leading to a resurgence of mining on the western edge of the Iron Range, between Grand Rapids and Hibbing.
At the forefront is a company called Magnetation, which is building its fourth plant outside Grand Rapids. In what old mining companies considered junk rock, Matt Lehtinen, the company's 32-year-old president, sees opportunity.
Turn Up Your Support
MPR News helps you turn down the noise and build shared understanding. Turn up your support for this public resource and keep trusted journalism accessible to all.
"Behind me here is actually a stockpile of waste iron ore called coarse tailings, about 400,000 tons of high grade waste, that 50 years ago was waste, but now is actually considered high grade feed for us for this plant," he said.
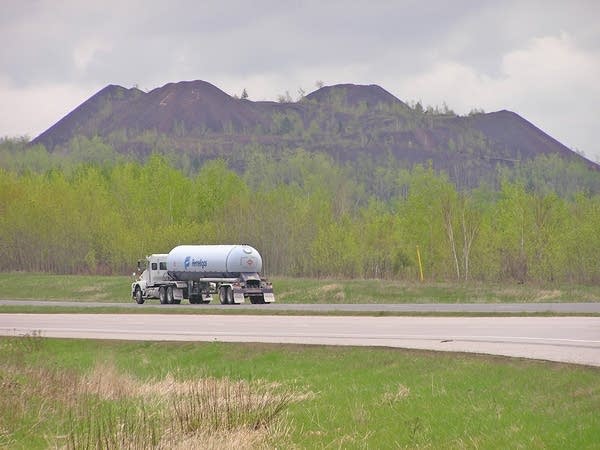
When the new plant opens in January, it will be supplied by two nearby tailings basins left behind by US Steel in the 1980s. Together, they cover about 300 football fields, stacked 60 feet tall with old mine waste.
At another nearby tailings dump the company is actively mining, an excavator is dumping what looks like fine black dirt into a 40 ton haul truck.
"That material is going to be hauled to the plant," Lehtinen said. "We're going to extract the remaining iron oxide, iron ore product out of it, and make a high value concentrate."
Mining companies have clawed iron ore out of this swath of northeast Minnesota since the 1880s -- first high grade "red" or "natural" ore, then lower grade taconite ore. After years of tinkering, Magnetation has figured out an innovative way to economically process the still lower grade ore left behind, with a five-story machine the company calls a Rev 3 Separator, which uses permanent magnets to extract the iron ore.
A water spray then washes out the iron ore into the bottom of the machine where it's collected, dried and eventually shipped to a steelmaker in Mexico. Soon, the ore will go to a pellet plant Magnetation is building in Indiana with its partner AK Steel.
Lehtinen said Magnetation has an advantage in that the material it's digging up has been mined before.
"We're able to compete against the big boys because we don't have to spend as much money on the drilling and blasting and crushing," he said. "We're mining a material that's already quite fine, and taking advantage of that carbon footprint, that energy that was put into it 50 years ago in some cases."
Lehtinen said because the company is not working in undisturbed areas, and its facilities don't create water discharges or air emissions, it can obtain permits quickly.
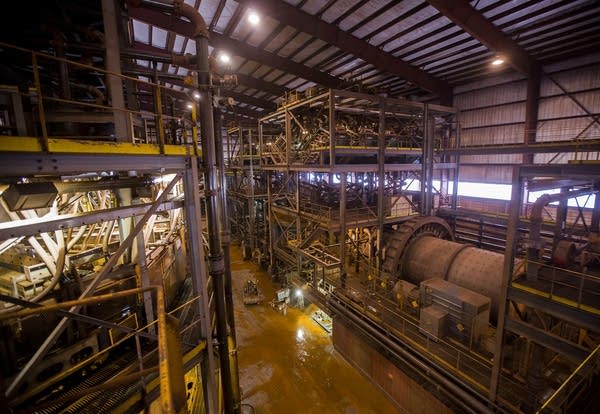
"Had our original permitting process taken two months longer, we wouldn't be here today because our first plant was funded and financed right before the Great Recession of 2008," he said. "So had we been just a few months late on our permitting, none of this would be here."
Magnetation is part of a growing effort to recover iron ore and other minerals from leftover tailings, said Pat Taylor, a professor of chemical metallurgy at the Colorado School of Mines.
"Part of it is the prices of many commodities have increased drastically, part is there's a very large expense with developing new mines," said Taylor, who teaches mineral processing. "So if you can find economic ways to treat material that's already been ground fine and still contains some values, it may have an economic benefit to do so."
Some companies are targeting scarce metals like germanium and gallium, used in cell phones, and other technologies that were left behind at old copper and zinc mines. But researchers are also finding new ways to extract the low-grade iron left behind in Minnesota, sometimes called "lean ore." Dick Kiesel, director of the Coleraine Minerals Research Lab that is part of the Natural Resources Research Institute at the University of Minnesota Duluth, said there's a lot there, even beyond what Magnetation is targeting.
"For example the University of Minnesota owns approximately 100 million tons of lean ore stockpiles on the Iron Range,"Kiesel said. "That's a significant carrot out there to at least pursue utilization of these piles."
Next year Magnetation's four plants combined will produce about four million tons of iron ore concentrate per year. That's a fraction of the 15 million tons per year the Iron Range's largest taconite plant, MinnTac, produces. But proportionately the company provides a lot of jobs -- over 400 in Minnesota when the new plant fires up.
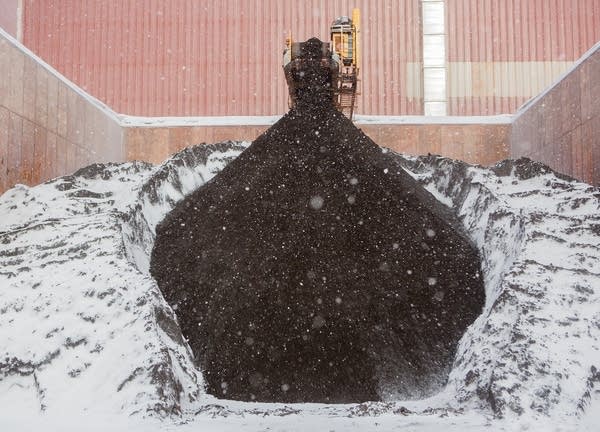
"Magnetation is really on the cutting edge of a rebirth of mining on the Western Mesabi," said state Rep. Tom Anzelc, DFL-Balsam Township, who helped Magnetation secure its initial seed financing from the state. "But I would not have expected it to grow so fast, and I certainly would not have expected them to employ as many people as they do."
But the company has experienced some growing pains. At certain times Magnetation's first plant near Keewatin sent huge clouds of dust into the air.
Two years ago the company paid the state a $40,000 fine and entered into a compliance agreement with the Pollution Control Agency.
Keewatin Mayor William King said that's solved the major dust problems. But he said the plant hasn't been the local economic boon he anticipated.
"I'm not real sure that we feel the impact locally here," King said. "We get some production tax, but it's not a great amount of money. I don't think it is what we thought it was going to be."
Still, the company was able to repay $5.5 million dollars in state loans from the state Department of Employment and Economic Development and the Iron Range Resources and Rehabilitation Board two years early, in January, 2012.
There's enough waste material and ore left behind in abandoned pits on the Iron Range to supply Magnetation for a century, Lehtinen said.
"Our goal," he said, "is sincerely to have a sustainable company where no one experiences a layoff during their career."