North Dakota researchers find cost-effective way to extract rare-earth elements from coal
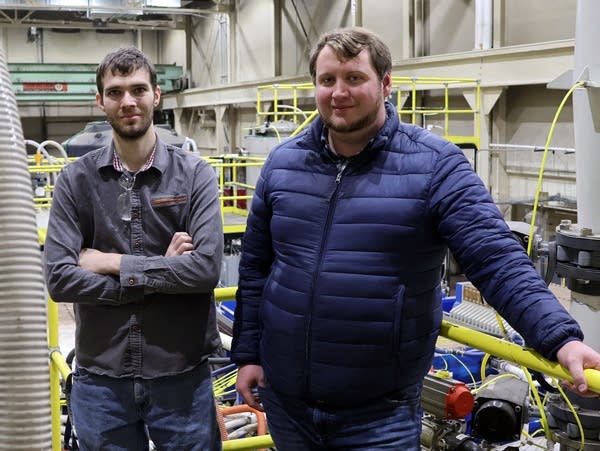
Go Deeper.
Create an account or log in to save stories.
Like this?
Thanks for liking this story! We have added it to a list of your favorite stories.
In a large warehouse in Grand Forks, Nicholas Dyrstad-Cincotta marvels at how far his team has come. Two years ago, they set out to test the economic viability of extracting critical metals from lignite coal, an abundant soft rock sediment found throughout North Dakota.
“We started with an open floor plan, roughly 10,000 square feet and nothing but a dream,” recalled Dyrstad-Cincotta who oversaw the construction of this plant and manages the daily operations.
Today, large tanks, car-sized filters and hundreds of sensors fill the warehouse floor. University of North Dakota researchers say this pilot project has already demonstrated that their idea is feasible, cost-effective and cleaner.
“We can do it a lot cheaper, a lot faster and also we can make sure we don’t get some of the problem impurities that would cause some of the environmental concerns later,” said senior research manager Nolan Theaker, referring to pollution associated with traditional hard rock mineral extraction methods.
Turn Up Your Support
MPR News helps you turn down the noise and build shared understanding. Turn up your support for this public resource and keep trusted journalism accessible to all.
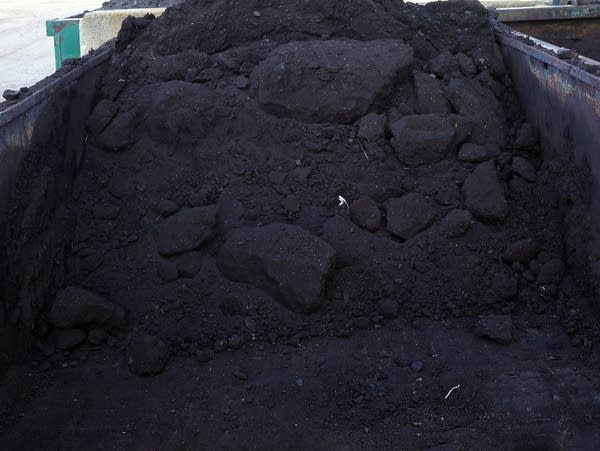
Critical mineral production in the U.S. is primarily done by mining hard rocks and using heat and powerful solvents to release the desired elements. The process generates large amounts of waste containing environmental toxins.
“We’re looking for secondary and unconventional sources like coal-based feed-stocks as really kind of a win-win,” said Grant Bromhal, senior science advisor with the U.S. Department of Energy. “We can relatively quickly extract rare earths and some other critical minerals that we found from materials that we've already dug out of the ground.”
Reducing dependence on China
Coal is a good fit for the U.S. strategy of finding cheaper, less environmentally damaging sources for critical minerals, said Bromhal, who also leads the DOE’s Minerals Sustainability division.
Over the past several decades the U.S. has become increasingly dependent on China as a critical mineral supplier. Earlier this year, China imposed restrictions on exports of germanium and gallium, two key minerals for the semiconductor industry.
“There is definitely an urgency,” said Bromhal. “We’ve been out of this game for a long time.”
In order to meet the growing demand for rare-earth minerals, the U.S. would need to build an entire infrastructure from mining to extraction to processing.
“We have some years to a decade to really start this out, but not much longer than that,” he said. “Our goal is to enable half of our rare-earth needs to be able to come from secondary and unconventional sources by 2035.”
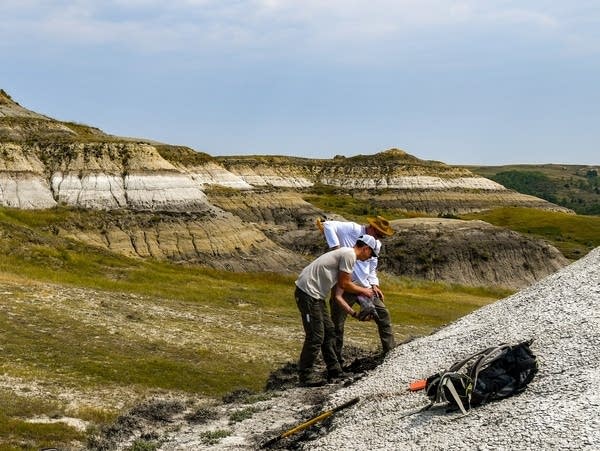
Lignite is a low-quality coal long used to fuel power plants in North Dakota. There are billions of tons of lignite in western and central parts of the state.
Rare-earth elements and minerals were captured in two zones within the coal deposits tens of millions of years ago.
‘Crazy climate event’
“There is this event at about 56 million years ago called The Paleocene-Eocene Thermal Maximum,” said geologist Levi Moxness with the North Dakota Geological Survey. “Volcanoes went off in the North Atlantic, and within a very short period of time global temperatures rose nine degrees Fahrenheit.”
The hot, humid climate created acidic conditions that leached minerals from rocks into the coal below.
“This crazy climate event 56 million years ago is responsible for one of those zones,” said Moxness.
The other zone likely developed through weathering of rock over a long period around 62 million years ago.
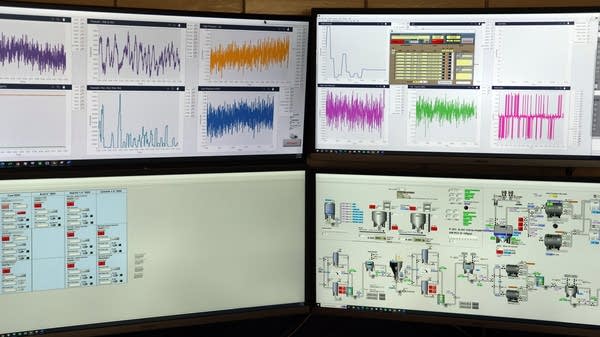
Many people doubted there were enough minerals in coal to make extraction economically viable. But UND researchers found they could remove the minerals more easily and more efficiently than expected.
“As of right now, we’re in a place where we're able to produce those rare-earth products at reasonable costs,” said Theaker, describing early results from the pilot project.
The coal being processed at this plant comes from waste stripped off the top of a coal seam mined to fuel power plants in western North Dakota.
The top of the coal contains too much clay to make a good fuel, but it is where the valuable minerals are concentrated.
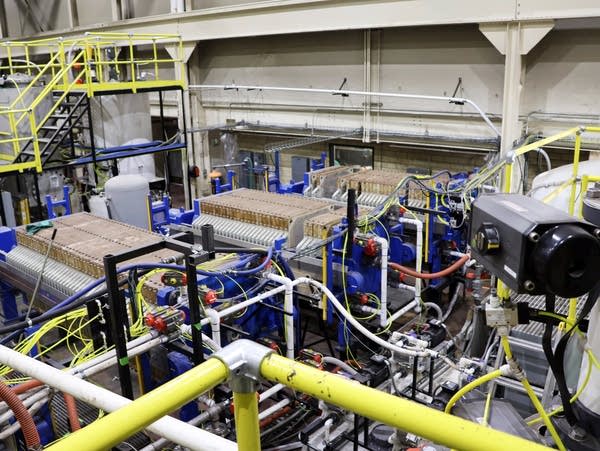
There are a total of 17 rare-earth elements. They are categorized from light to heavy.
“The heavy rare earths, which are much more valuable — some of them in the range of $1,000 per kilogram — can make up 50 percent of the total rare-earth elements (found in the deposits),” said Moxness.
Exceeding expectations
The Department of Energy previously used a ratio of 300 parts per million as the economically viable level for extracting rare-earth elements.
But North Dakota researchers found their process effective at half that concentration.
“The trick about rare-earths is if you had 50 parts per million of terbium, you have an absolute goldmine,” said Theaker. “Meanwhile, if you have a resource that's 500,000 parts per million cerium you won't even make money selling it. So, the distribution of those rare earths really is key.”
North Dakota, it seems, might benefit from the luck of the geologic draw.
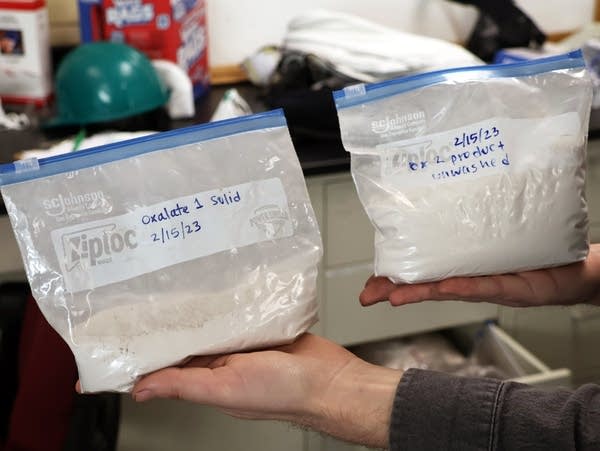
The North Dakota Geological Survey has collected about 2,000 samples from coal outside of existing mines and found rare-earth concentrations as high as 3,000 parts per million in thin coal seams.
But extracting that coal would require a lengthy permitting process to open a new mine.
Theaker said details of the extraction process are proprietary, but it uses a diluted acid to wash the minerals from the soft coal. He said the acid is about ten times more dilute than what is used in hard rock rare-earth extraction. Filters capture the minerals and the extracted material is shipped to a Nebraska company for processing.
The dried product, stored in a plastic bag, looks like baking soda. But it contains significant quantities of rare-earths.
“The important ones we produce are the ones used in magnets,” said Theaker. “The permanent magnets you see in EV motors, wind turbines, hard drives for your computer, the compass on your phone, and also compasses and gyroscopes for weapons systems.”
The coal extract also contains the minerals gallium and germanium, which are used in semi-conductors, and cobalt, which is used in batteries.
Theaker believes North Dakota coal could provide 30 to 50 percent of U.S. gallium and germanium demand.
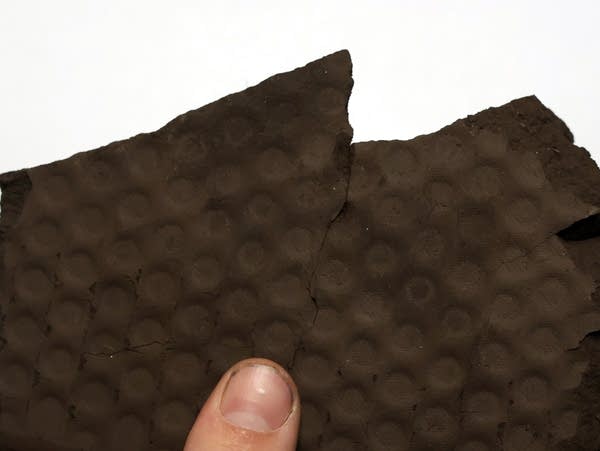
The coal that remains could be burned as fuel, but Theaker said it might be more valuable for other uses. The extraction process changes the lignite in a way that appears to make it a good source for light, strong bricks.
Researchers are still optimizing the pilot plant operation, but they are confident in the early results.
Theaker said they’re already working with an engineering firm to design the first commercial facility that would be built next to a western North Dakota coal mine.